What technological drivers will shape the petrochemical industry in the new millennium? Three key trends emerging in the latter part of the current century are likely to influence petrochemical process technologies into the 21st century:
The petrochemical industry grew to its current prominence largely in the 20th century. Indeed, the bulk of its market penetration and geographic spread from its beginnings in the US, Western Europe, and Japan occurred in the second half of the century, from 1950 onwards. It is therefore a young industry with much potential in the next century.
Over a decade ago, Frank Popoff, then CEO of The Dow Chemical Co., predicted that chemical industry ownership would shrink to a few very large integrated firms in each region. The petrochemical industry is a large, if not the largest, segment of the global chemical industry, and Popoff's forecast could equally well apply.
Will the new century bring the changes that Popoff forecast?
Some, like Hoechst AG, ICI plc, and Monsanto Co., chose to exit petrochemicals. Those firms concluded that their existing production base was uncompetitive in the newly globalizing world, and that their capital would be better rewarded in life sciences, pharmaceuticals, and specialties.
Some, with a strong commitment to the industry, are aggressively seeking competitive advantages in countries and regions with low feedstock costs, which offer huge market potential. These include Borealis, Dow (with Union Carbide Corp.), and Exxon Chemical Co. (with Mobil Chemical Co.).
Companies such as Huntsman Corp. have used venture capital to build new businesses on the divestments of others. Venture capital groups have also made use of low valuations in times of recession to build petrochemical portfolios.
Finally, state-owned companies in the hydrocarbon-rich areas of the world, such as the Middle East, Malaysia, and Venezuela, are adding value to their national resources through petrochemical routes.
With such diverse strategies, the petrochemical industry of the 21st century is unlikely to continue the consolidation trends of the 20th century. Instead, it will bring diversity of industry participants, feedstock, and processes.
New entrants and existing industry participants will spread the global industry's asset base into diverse regions, following either the downstream market for derivatives or favored feedstock prices.
In the next century, two process technology developments should enable an expansion of the methane-value chain to include production of chemicals now made by conventional petrochemical routes: new natural gas reforming technology and larger scale methanol units.
New reactor technology for natural gas reforming to make precursor synthesis gas (syngas), a mixture of hydrogen and carbon monoxide, promises to reduce both capital and operating costs. Improved costs will result in improved economics for ensuing downstream products.
Sources of natural gas reformer technologies include a joint development by BP Amoco plc and Kvaerner and a separate effort by ICI (the Advanced Gas Heated Reformer).
Improved methanol production economics are also expected through commercialization of very large-scale, single-train production units.
Typically, world-scale methanol plants are 2,500 tonne/day facilities. Methanol technology licensors, including Toyo Engineering Corp., Lurgi AG, Kvaerner, and ICI, are developing the capability to double the size of single train methanol units to 5,000 tonnes/day.
Cost savings from new syngas reactor technology combined with the large economy of scale derived from very large methanol units will drive down costs of methanol.
Improved syngas and methanol economics will renew interest in the development of C1-based petrochemical process technology. Of course, a C1-based chemical industry is not a new idea. Two separate dislocations caused the industry to move previously in this direction.
The first dislocation was World War II. Germany's lack of access to liquid petroleum feedstock for fuel and chemicals prompted German scientists and engineers to develop alternative means of making liquid fuels, which led to the development of the Fischer-Tropsch reaction that converted syngas from coal to liquid fuels.
The second dislocation occurred in the mid 1970s and early 1980s when the price of oil skyrocketed. The petrochemical industry, among others, reacted by launching development programs to convert syngas from coal directly to chemicals. As oil prices collapsed, however, many companies abandoned these programs.
Now, once again, it seems the industry is moving towards development of chemicals and fuels from syngas, not derived from coal but from natural gas. Unlike in the past, economics is driving this renewed interest. Dislocations, such as a war or cartel restrictions, can disappear as fast as they appear. Good economics, stemming from technological innovation and market expansion into developing countries, however, is the basis of a more sustainable interest.
In the liquid-fuels area, there is increased interest in new process chemistry and engineering. New entrepreneurial companies, such as Syntroleum Corp. and Rentech Inc., have joined the traditionally active companies, such as Sasol, Shell, and Exxon Corp., as technology developers.
In the chemicals arena, UOP and Norsk Hydro ASA have made good progress in converting methanol-to-olefins (MTO). While this route is not yet competitive with conventional petroleum-based sources of olefins at the current price of oil, it will not take too much of a rise of oil prices or too much imagination to make MTO processes attractive in the new millennium.
Key derivatives of methanol, such as formaldehyde and acetic acid, will also benefit from lower methanol costs.
In fact it is interesting to speculate that some old chemistry may become economic again. For example, a route to ethylene glycol that was practiced by E.I. du Pont de Nemours & Co. (DuPont) until 1968 was based completely on C1 chemistry. This route, owing to anticipated lower costs along the entire methane-value chain, may yet find a new lease on life in the 21st century.
Acetic acid production via methanol carbonylation technology has had some recent dramatic cost improvements.
The Celanese "low water" process and the BP Amoco iridium catalyzed Cativa process have each allowed acetic acid plants to double or even triple in capacity with very little additional capital. This has allowed fixed costs per pound to be significantly reduced. Acetic acid cash cost by these new world class mega-plants is as low as 7-8 ¢/lb.
Acetic acid at such low costs makes it an interesting candidate as a feedstock to make other chemicals, which makes it a key material in building up a C1-based chemical industry.
A particularly interesting notion is conversion of low cost acetic acid by hydrogenolysis to ethanol. This may be of interest with regard to the use of ethanol as a potential replacement for MTBE as an environmentally safe oxygenate for fuel.
Fig. 1 shows other potential chemicals that can be envisioned as part of the links in the 21st century methane-value chain.
Chemical engineers translated the high yield reaction chemistry into relatively simple plant designs with limited need for recycle streams or complex separation/purification schemes. Safety issues involved with handling large volumes of acetylene and its expense are big problems with acetylene based process chemistry, however.
The high reactivity of acetylene, moreover, does not come cheap. Putting the triple bond into acetylene required much energy and hence expense. This expense was unavoidably passed on to any downstream products.
The advent of selective transition metal oxidation catalysts enabled olefins to replace acetylene as the major feedstock. This ushered in a new era of petrochemical process technology in the 1960s and 1970s. The industry is still reliant on olefin feedstocks for most monomers.
While the development of "smart" olefin oxidation catalysts was the key to moving the industry away from expensive and dangerous acetylene, many engineering developments were required to allow successful large scale commercialization of olefin-based processes.
These developments included the handling of the high levels of heat from reaction exotherms, difficult separations from the inherently lower selectivities achieved, avoidance of feedstock/oxygen explosion regimes, catalyst fouling issues, and materials of construction concerns from the typically higher temperature operation coupled with corrosive reaction environments.
In the new millennium, the next phase of the chemical industry's drive to use cheaper feedstocks will be the use of alkanes (e.g. methane, ethane, propane, butane). The direct conversion of alkanes, using transition metal catalysis, into chemicals has been the subject of research and development efforts as long as 30-40 years ago.
The technical challenges for the direct conversion of alkanes to chemicals are formidable. Unlike acetylene and olefins, there is no ready "handle" in alkanes for catalyst designers to target. In addition, the engineering challenges will likely be even more challenging than the issues encountered in commercializing olefins-based processes.
Almost certainly, reaction conversions per pass will be relatively low to try and maintain acceptable selectivities. This will require extensive recycle streams and associated equipment. The potential certainly exists for production of over-oxidation products, such as carbon oxides, which will cause environmental concerns.
In addition, these processes may require fairly exotic materials of construction as reaction temperatures and corrosive catalyst promoters may be needed.
All of these factors will lead to increased capital intensity. Successful development of alkane-activation technologies may require the cost advantage of employing low cost alkane feedstock to offset the higher capital investment. Fig. 2 summarizes these issues.
Probably the most notable success story in alkane-activation technology is the conversion of n-butane to maleic anhydride. This process was first commercialized by Amoco using a Chem Systems process in 1975.
It is interesting to note that 25 years later, this process is still the only example of a commercially operated transition metal catalyzed alkane-oxidation process for a commodity chemical. Perhaps the reason for this is not so much that n-butane is easier to activate than other alkanes, but rather the product, maleic anhydride, is both thermodynamically and confirmationally highly stable. In essence, maleic anhydride is a thermodynamic and kinetic "well" and it might be surprising to avoid its formation.
A spin-off of the success of the n-butane to maleic anhydride process is technology to further react the maleic anhydride, acid, or maleate esters to 1,4-butanediol and tetrahydrofuran. These products had for many years been exclusively made from acetylene based processes. They find use in spandex fibers, engineering polymers, and specialty solvents and water-soluble polymers.
Now several companies, including Kvaerner, BP Amoco/Lurgi, and a small entrepreneurial Italian company, Sisas, have leveraged their success in alkane-activation technology and extended their reach downstream into higher value 1,4-buanediol and tetrahydrofuran.
Two alkane-activation technologies, now very close to commercialization, are likely to be commercialized in the early part of the 21st century.
One process is European Vinyl Corp.'s (EVC) ethane to vinyl chloride monomer (VCM) process. EVC recently announced its intent to build a commercial-scale plant.
The current process for making VCM is a complicated multi-step sequence for converting ethylene to VCM. Many previous attempts to develop an ethane-based process failed as the temperatures required to activate ethane resulted in low selectivities of VCM and severe corrosion problems.
The key to the new EVC ethane to VCM process is development of a catalyst that is active at relatively low temperatures, which avoids the severe corrosion problems and reaction by-products.
The other process that appears very close to commercialization is propane to acrylonitrile. BP Amoco, Asahi, and Mitsubishi Chemical are independently developing this type of process. Chem Systems' assessment of the current state of such a process indicates that the economics of the propane based route are only marginally superior to the conventional based propylene route.
In any economic analysis of alkane-activation technologies, however, it is necessary to look not just at the prices of the alkanes but to consider the price differential between the alkane and corresponding olefin in the region of the world where the technology is to be employed.
The long-range forecast is for high demand for propylene as a result of strong demand for polypropylene. This will lead to higher pricing for propylene and will tend to make the economics of a propane-based process technology more attractive.
Other alkane-activation technologies which are candidates for commercialization in the early part of the 21st century include ethane to acetic acid, isobutane to methyl methacrylate, catalytic ethane dehydrogenation to ethylene, and propane to acrylic acid.
Table 1 summarizes current, imminent, and prospective ethane-activation technologies.
Today, innovations in biotechnology are moving from the fine and performance chemicals arena to commodity chemicals and even refining. In the past, chemical companies did not commonly use molecular biology to engineer a desired biological system for a commercial process. Companies traditionally viewed biotechnology as an activity beyond the province of chemical companies and best left to small specialist organizations.
Chemical and mechanical engineering challenges for bioengineering will, in many cases, be very different from the typical processing issues faced in developing conventional petrochemical processes.
For example, biotech processes generally must deal with low concentration aqueous solutions of microbes, feedstocks, and end-products. In addition, reaction rates are often low as compared to classical catalytic petrochemical reaction rates.
These features will require the know-how to economically manage large volumes of water, including isolation of end-products from water, without incurring huge energy costs. Energy costs come from vaporizing copious quantities of water, exposing sensitive bio-catalysts to harsh conditions, and clean-up of waste water streams for environmentally safe disposal.
For commercial technology precedents in operating design and protocols to cope with these challenges, the developing bioprocessing sector may find it helpful to look to other industry segments such as food and beverage processing, pulp and paper, and pharmaceuticals.
A very promising technology under development by a number of new start-up companies, such as Diversa Corp. and ThermoGen Inc., is the incorporation of genetic material from "extremophiles" for developing temperature resistant bio-catalysts to cope with the harsh conditions needed for commercial chemical or petroleum processing.
Extremophiles are naturally occurring organisms prospected and mined from extreme environments such as geysers, hot springs, ocean vents, brine ponds, polar ice caps, and even polluted water bodies. These organisms can withstand very harsh environments. With this characteristic, they might be used to genetically alter other bio-catalysts lacking the ability to withstand harsh processing conditions.
Despite these challenges, many large and historically petrochemical-based corporations are extending their reach into biotechnology and the life sciences. DuPont, Hoechst, DSM, Rhone-Poulenc, and Dow have all declared that biotechnology and the life sciences are major thrust areas for them. These companies may lead the biotech revolution in the chemical and petroleum areas in the new millennium.
The combined effect of market demand and technological advances has led to a number of emerging applications of biotechnology based chemical manufacture in different industry segments. These technologies are moving at different paces and have different prospects for commercialization (Table 2).
One exciting development is DuPont's and Genecor's joint development effort for making a new monomer, 1,3-propanediol (PDO) from glucose through the use of genetically altered microbes. PDO finds application in high performance polyester fibers.
Based on information from DuPont patents, Chem Systems has assessed the economics of a speculative biotech PDO process in comparison to the new ethylene-based route recently commercialized by Shell Chemical and the older propylene route used by Degussa (recently acquired by DuPont to ensure short term developmental quantities of PDO until their biotech route is perfected).
As shown in Fig. 3, the biotech route has the potential to be competitive with Shell's ethylene-based route. If the biotech route reaches full-scale commercialization in the 21st century it will be the first example of a biotech route being competitive with a petrochemical route for a large volume monomer. DuPont still faces many scale-up challenges before full scale commercialization can begin, however.
Biotechnology will also impact the petroleum production and refining industries in the new millennium. Currently, there are widely varying interest levels by companies and governments around the world. A few companies have independent efforts underway to develop biotech-based technologies in petroleum refining or upgrading. A number of large companies are however participating in government-led R&D consortia or parnterships. Interests fall into three primary areas: crude upgrading, refining processes, and environmental spill remediation and plant-waste treatment.
Texaco, Koch, Total Raffinage, Kellogg Brown & Root, Petrostar and Petrolite have been involved in varying degrees in Energy BioSystems' development program for commercializing biodesulfurization of distillate fractions. Oak Ridge National Laboratories is involved with a number of large petroleum companies in the development of biotech enabled crude upgrading. In Japan, PEC and MITI are involved with about 12 Japanese companies in a large program focussed on diesel biodesulfurization. Other efforts in biodesulfurization are going on in Italy, Spain, Canada, and South Korea.
The use of biotechnology in oil field production is also finding some application. Halliburton recently announced that it will use a heat tolerant enzyme, developed by Diversa, in conjunction with conventional fracturing fluids to cost effectively increase oil production. The enzyme was discovered in an extremophile located in a hydrothermal vent off the coast of Vulcano, Italy.
Source: ogj.com
#petroleum #Petrochemistry2018 #Petrochemistryconferences #Petrochemistryupdates #oil #gas #exploration #chemicalconferences #LasVegas #USA
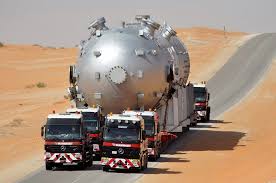
- Extending the methane-value chain.
- Alkane-activation technologies.
- Biotechnology.
The petrochemical industry grew to its current prominence largely in the 20th century. Indeed, the bulk of its market penetration and geographic spread from its beginnings in the US, Western Europe, and Japan occurred in the second half of the century, from 1950 onwards. It is therefore a young industry with much potential in the next century.
Over a decade ago, Frank Popoff, then CEO of The Dow Chemical Co., predicted that chemical industry ownership would shrink to a few very large integrated firms in each region. The petrochemical industry is a large, if not the largest, segment of the global chemical industry, and Popoff's forecast could equally well apply.
Will the new century bring the changes that Popoff forecast?
Industry structure
Global trends and fundamental shifts in competitive advantage characterized the petrochemical industry of the past decade. The emerging patterns form the basis of the industry in the 21st century. They include globalization, free trade, and the mobility of capital.- Globalization. Markets and supply chains today demand the best and most sophisticated products, regardless of location. Product and process innovations are no longer initially reserved for the large sophisticated markets of the U.S., Western Europe, and Japan.
- Free trade. The second half of the 20th century ushered in the successful opening up of global trade by GATT (General Agreement on Tariffs & Trade) and the WTO (World Trade Organization) from the sclerotic regulations of the recessionary thirties.
- Mobility of capital. The mobility of capital is perhaps a subset of globalization, but it has and will continue to facilitate the establishment of new producers and new regional business opportunities.
Some, like Hoechst AG, ICI plc, and Monsanto Co., chose to exit petrochemicals. Those firms concluded that their existing production base was uncompetitive in the newly globalizing world, and that their capital would be better rewarded in life sciences, pharmaceuticals, and specialties.
Some, with a strong commitment to the industry, are aggressively seeking competitive advantages in countries and regions with low feedstock costs, which offer huge market potential. These include Borealis, Dow (with Union Carbide Corp.), and Exxon Chemical Co. (with Mobil Chemical Co.).
Companies such as Huntsman Corp. have used venture capital to build new businesses on the divestments of others. Venture capital groups have also made use of low valuations in times of recession to build petrochemical portfolios.
Finally, state-owned companies in the hydrocarbon-rich areas of the world, such as the Middle East, Malaysia, and Venezuela, are adding value to their national resources through petrochemical routes.
With such diverse strategies, the petrochemical industry of the 21st century is unlikely to continue the consolidation trends of the 20th century. Instead, it will bring diversity of industry participants, feedstock, and processes.
New entrants and existing industry participants will spread the global industry's asset base into diverse regions, following either the downstream market for derivatives or favored feedstock prices.
Methane-value chain
As previously discussed, process technology is no longer reserved for the large sophisticated markets of the U.S., Western Europe, and Japan. As natural gas resources are being discovered in various remote regions of the world, local governments want to monetize these resources by converting the otherwise stranded natural gas into transportable commodities such as methanol, ammonia, and possibly liquid fuels.In the next century, two process technology developments should enable an expansion of the methane-value chain to include production of chemicals now made by conventional petrochemical routes: new natural gas reforming technology and larger scale methanol units.
New reactor technology for natural gas reforming to make precursor synthesis gas (syngas), a mixture of hydrogen and carbon monoxide, promises to reduce both capital and operating costs. Improved costs will result in improved economics for ensuing downstream products.
Sources of natural gas reformer technologies include a joint development by BP Amoco plc and Kvaerner and a separate effort by ICI (the Advanced Gas Heated Reformer).
Improved methanol production economics are also expected through commercialization of very large-scale, single-train production units.
Typically, world-scale methanol plants are 2,500 tonne/day facilities. Methanol technology licensors, including Toyo Engineering Corp., Lurgi AG, Kvaerner, and ICI, are developing the capability to double the size of single train methanol units to 5,000 tonnes/day.
Cost savings from new syngas reactor technology combined with the large economy of scale derived from very large methanol units will drive down costs of methanol.
Improved syngas and methanol economics will renew interest in the development of C1-based petrochemical process technology. Of course, a C1-based chemical industry is not a new idea. Two separate dislocations caused the industry to move previously in this direction.
The first dislocation was World War II. Germany's lack of access to liquid petroleum feedstock for fuel and chemicals prompted German scientists and engineers to develop alternative means of making liquid fuels, which led to the development of the Fischer-Tropsch reaction that converted syngas from coal to liquid fuels.
The second dislocation occurred in the mid 1970s and early 1980s when the price of oil skyrocketed. The petrochemical industry, among others, reacted by launching development programs to convert syngas from coal directly to chemicals. As oil prices collapsed, however, many companies abandoned these programs.
Now, once again, it seems the industry is moving towards development of chemicals and fuels from syngas, not derived from coal but from natural gas. Unlike in the past, economics is driving this renewed interest. Dislocations, such as a war or cartel restrictions, can disappear as fast as they appear. Good economics, stemming from technological innovation and market expansion into developing countries, however, is the basis of a more sustainable interest.
In the liquid-fuels area, there is increased interest in new process chemistry and engineering. New entrepreneurial companies, such as Syntroleum Corp. and Rentech Inc., have joined the traditionally active companies, such as Sasol, Shell, and Exxon Corp., as technology developers.
In the chemicals arena, UOP and Norsk Hydro ASA have made good progress in converting methanol-to-olefins (MTO). While this route is not yet competitive with conventional petroleum-based sources of olefins at the current price of oil, it will not take too much of a rise of oil prices or too much imagination to make MTO processes attractive in the new millennium.
Key derivatives of methanol, such as formaldehyde and acetic acid, will also benefit from lower methanol costs.
In fact it is interesting to speculate that some old chemistry may become economic again. For example, a route to ethylene glycol that was practiced by E.I. du Pont de Nemours & Co. (DuPont) until 1968 was based completely on C1 chemistry. This route, owing to anticipated lower costs along the entire methane-value chain, may yet find a new lease on life in the 21st century.
Acetic acid production via methanol carbonylation technology has had some recent dramatic cost improvements.
The Celanese "low water" process and the BP Amoco iridium catalyzed Cativa process have each allowed acetic acid plants to double or even triple in capacity with very little additional capital. This has allowed fixed costs per pound to be significantly reduced. Acetic acid cash cost by these new world class mega-plants is as low as 7-8 ¢/lb.
Acetic acid at such low costs makes it an interesting candidate as a feedstock to make other chemicals, which makes it a key material in building up a C1-based chemical industry.
A particularly interesting notion is conversion of low cost acetic acid by hydrogenolysis to ethanol. This may be of interest with regard to the use of ethanol as a potential replacement for MTBE as an environmentally safe oxygenate for fuel.
![]() |
Alkane activation
After World War II, acetylene was the key starting feedstock for many large volume monomers. Acetylene's highly reactive triple bond provided a ready "handle" for chemists to grab onto for designing process chemistry.Chemical engineers translated the high yield reaction chemistry into relatively simple plant designs with limited need for recycle streams or complex separation/purification schemes. Safety issues involved with handling large volumes of acetylene and its expense are big problems with acetylene based process chemistry, however.
The high reactivity of acetylene, moreover, does not come cheap. Putting the triple bond into acetylene required much energy and hence expense. This expense was unavoidably passed on to any downstream products.
The advent of selective transition metal oxidation catalysts enabled olefins to replace acetylene as the major feedstock. This ushered in a new era of petrochemical process technology in the 1960s and 1970s. The industry is still reliant on olefin feedstocks for most monomers.
While the development of "smart" olefin oxidation catalysts was the key to moving the industry away from expensive and dangerous acetylene, many engineering developments were required to allow successful large scale commercialization of olefin-based processes.
These developments included the handling of the high levels of heat from reaction exotherms, difficult separations from the inherently lower selectivities achieved, avoidance of feedstock/oxygen explosion regimes, catalyst fouling issues, and materials of construction concerns from the typically higher temperature operation coupled with corrosive reaction environments.
In the new millennium, the next phase of the chemical industry's drive to use cheaper feedstocks will be the use of alkanes (e.g. methane, ethane, propane, butane). The direct conversion of alkanes, using transition metal catalysis, into chemicals has been the subject of research and development efforts as long as 30-40 years ago.
The technical challenges for the direct conversion of alkanes to chemicals are formidable. Unlike acetylene and olefins, there is no ready "handle" in alkanes for catalyst designers to target. In addition, the engineering challenges will likely be even more challenging than the issues encountered in commercializing olefins-based processes.
Almost certainly, reaction conversions per pass will be relatively low to try and maintain acceptable selectivities. This will require extensive recycle streams and associated equipment. The potential certainly exists for production of over-oxidation products, such as carbon oxides, which will cause environmental concerns.
In addition, these processes may require fairly exotic materials of construction as reaction temperatures and corrosive catalyst promoters may be needed.
![]() |
Probably the most notable success story in alkane-activation technology is the conversion of n-butane to maleic anhydride. This process was first commercialized by Amoco using a Chem Systems process in 1975.
It is interesting to note that 25 years later, this process is still the only example of a commercially operated transition metal catalyzed alkane-oxidation process for a commodity chemical. Perhaps the reason for this is not so much that n-butane is easier to activate than other alkanes, but rather the product, maleic anhydride, is both thermodynamically and confirmationally highly stable. In essence, maleic anhydride is a thermodynamic and kinetic "well" and it might be surprising to avoid its formation.
A spin-off of the success of the n-butane to maleic anhydride process is technology to further react the maleic anhydride, acid, or maleate esters to 1,4-butanediol and tetrahydrofuran. These products had for many years been exclusively made from acetylene based processes. They find use in spandex fibers, engineering polymers, and specialty solvents and water-soluble polymers.
Now several companies, including Kvaerner, BP Amoco/Lurgi, and a small entrepreneurial Italian company, Sisas, have leveraged their success in alkane-activation technology and extended their reach downstream into higher value 1,4-buanediol and tetrahydrofuran.
Two alkane-activation technologies, now very close to commercialization, are likely to be commercialized in the early part of the 21st century.
One process is European Vinyl Corp.'s (EVC) ethane to vinyl chloride monomer (VCM) process. EVC recently announced its intent to build a commercial-scale plant.
The current process for making VCM is a complicated multi-step sequence for converting ethylene to VCM. Many previous attempts to develop an ethane-based process failed as the temperatures required to activate ethane resulted in low selectivities of VCM and severe corrosion problems.
The key to the new EVC ethane to VCM process is development of a catalyst that is active at relatively low temperatures, which avoids the severe corrosion problems and reaction by-products.
The other process that appears very close to commercialization is propane to acrylonitrile. BP Amoco, Asahi, and Mitsubishi Chemical are independently developing this type of process. Chem Systems' assessment of the current state of such a process indicates that the economics of the propane based route are only marginally superior to the conventional based propylene route.
In any economic analysis of alkane-activation technologies, however, it is necessary to look not just at the prices of the alkanes but to consider the price differential between the alkane and corresponding olefin in the region of the world where the technology is to be employed.
The long-range forecast is for high demand for propylene as a result of strong demand for polypropylene. This will lead to higher pricing for propylene and will tend to make the economics of a propane-based process technology more attractive.
Other alkane-activation technologies which are candidates for commercialization in the early part of the 21st century include ethane to acetic acid, isobutane to methyl methacrylate, catalytic ethane dehydrogenation to ethylene, and propane to acrylic acid.
![]() |
Biotechnology
Biotechnology is increasingly finding use throughout the fine chemical, pharmaceutical, and agrochemical business sectors.Today, innovations in biotechnology are moving from the fine and performance chemicals arena to commodity chemicals and even refining. In the past, chemical companies did not commonly use molecular biology to engineer a desired biological system for a commercial process. Companies traditionally viewed biotechnology as an activity beyond the province of chemical companies and best left to small specialist organizations.
Chemical and mechanical engineering challenges for bioengineering will, in many cases, be very different from the typical processing issues faced in developing conventional petrochemical processes.
For example, biotech processes generally must deal with low concentration aqueous solutions of microbes, feedstocks, and end-products. In addition, reaction rates are often low as compared to classical catalytic petrochemical reaction rates.
These features will require the know-how to economically manage large volumes of water, including isolation of end-products from water, without incurring huge energy costs. Energy costs come from vaporizing copious quantities of water, exposing sensitive bio-catalysts to harsh conditions, and clean-up of waste water streams for environmentally safe disposal.
For commercial technology precedents in operating design and protocols to cope with these challenges, the developing bioprocessing sector may find it helpful to look to other industry segments such as food and beverage processing, pulp and paper, and pharmaceuticals.
A very promising technology under development by a number of new start-up companies, such as Diversa Corp. and ThermoGen Inc., is the incorporation of genetic material from "extremophiles" for developing temperature resistant bio-catalysts to cope with the harsh conditions needed for commercial chemical or petroleum processing.
Extremophiles are naturally occurring organisms prospected and mined from extreme environments such as geysers, hot springs, ocean vents, brine ponds, polar ice caps, and even polluted water bodies. These organisms can withstand very harsh environments. With this characteristic, they might be used to genetically alter other bio-catalysts lacking the ability to withstand harsh processing conditions.
Despite these challenges, many large and historically petrochemical-based corporations are extending their reach into biotechnology and the life sciences. DuPont, Hoechst, DSM, Rhone-Poulenc, and Dow have all declared that biotechnology and the life sciences are major thrust areas for them. These companies may lead the biotech revolution in the chemical and petroleum areas in the new millennium.
![]() |
One exciting development is DuPont's and Genecor's joint development effort for making a new monomer, 1,3-propanediol (PDO) from glucose through the use of genetically altered microbes. PDO finds application in high performance polyester fibers.
Based on information from DuPont patents, Chem Systems has assessed the economics of a speculative biotech PDO process in comparison to the new ethylene-based route recently commercialized by Shell Chemical and the older propylene route used by Degussa (recently acquired by DuPont to ensure short term developmental quantities of PDO until their biotech route is perfected).
![]() |
Biotechnology will also impact the petroleum production and refining industries in the new millennium. Currently, there are widely varying interest levels by companies and governments around the world. A few companies have independent efforts underway to develop biotech-based technologies in petroleum refining or upgrading. A number of large companies are however participating in government-led R&D consortia or parnterships. Interests fall into three primary areas: crude upgrading, refining processes, and environmental spill remediation and plant-waste treatment.
Texaco, Koch, Total Raffinage, Kellogg Brown & Root, Petrostar and Petrolite have been involved in varying degrees in Energy BioSystems' development program for commercializing biodesulfurization of distillate fractions. Oak Ridge National Laboratories is involved with a number of large petroleum companies in the development of biotech enabled crude upgrading. In Japan, PEC and MITI are involved with about 12 Japanese companies in a large program focussed on diesel biodesulfurization. Other efforts in biodesulfurization are going on in Italy, Spain, Canada, and South Korea.
The use of biotechnology in oil field production is also finding some application. Halliburton recently announced that it will use a heat tolerant enzyme, developed by Diversa, in conjunction with conventional fracturing fluids to cost effectively increase oil production. The enzyme was discovered in an extremophile located in a hydrothermal vent off the coast of Vulcano, Italy.
Source: ogj.com
#petroleum #Petrochemistry2018 #Petrochemistryconferences #Petrochemistryupdates #oil #gas #exploration #chemicalconferences #LasVegas #USA
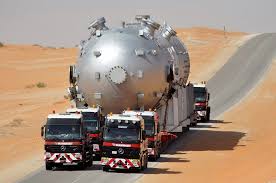
No comments:
Post a Comment